About Yamanaka NuriFeatures of Yamanaka Lacquerware
Yamanaka is one of the three major lacquerware production areas in the prefecture, along with Wajima for lacquering and Kanazawa for makie. Yamanaka has long been home to a large number of Kijiji-shi (woodworkers)* and boasts the highest production of hikimono (ground woodwork)* in the country.
A major characteristic of Yamanaka lacquerware, which makes use of grain patterns and expresses natural textures, is the tatekidori technique, in which the bowl is shaped in the direction in which the wood grows. This produces robust lacquerware that is resistant to distortion due to drying, and enables elaborate finishing not only of bowls but also of thinly ground pieces and lids. Furthermore, the decorative grinding*, which produces various patterns on the wood, such as sen-suji and ara-suji, gives birth to Yamanaka-nuri lacquerware with its unique attention to detail.
*Hikimono kinjiki: techniques and products for making vessels and decorations by grinding wood with a rotating wheel and a blade.
*Decorative grinding: a technique for decorating the surface of the wood with parallel stripes, spiral lines and other patterns.
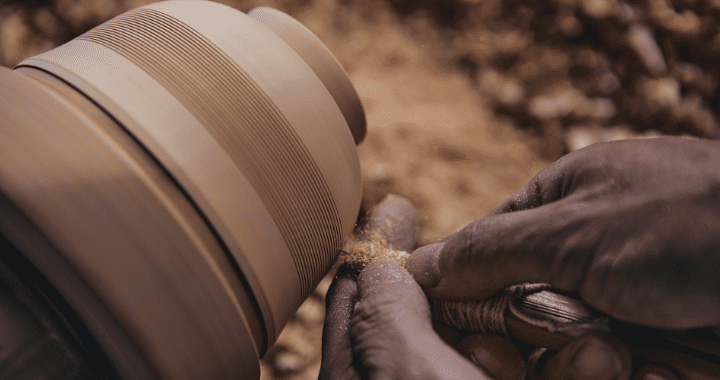
Japan's best rokuro techniques' supported by craftsmen.
Many woodworkers are active in Yamanaka, including Ryozo Kawakita, the first woodworker to be recognised as a Living National Treasure. The craftsmen's advanced skills have given rise to a variety of techniques, such as thin-hewn to make the wood so thin that light can see through it, and decorative hewn to carve delicate patterns on the wood surface. All the blades used for grinding are made by craftsmen who forge the steel. The relentless pursuit of sharpness underpins Japan's best roroku techniques.
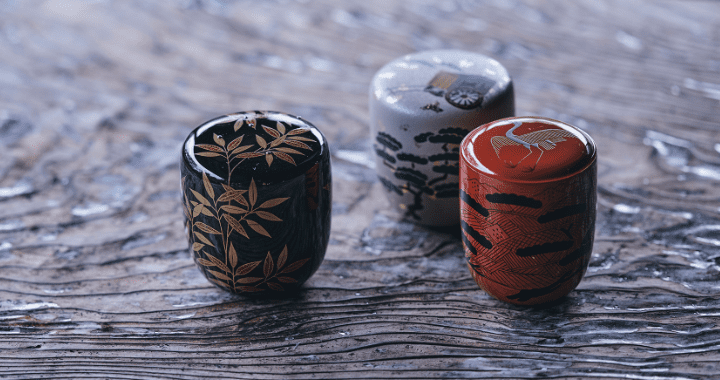
Advanced makie technology' as typified by tea utensils.
makie is a technique for drawing patterns on lacquered vessels using gold, silver or coloured powders. makie technique was introduced to Yamanaka-nuri around the middle of the Edo period. Takamakie, in which only the makie portion on top of the lacquer base is raised high, is well known. Delicate, three-dimensional makie designs on black or bright vermilion lacquer are applied not only to tea ceremony utensils, but also to accessories and stationery.
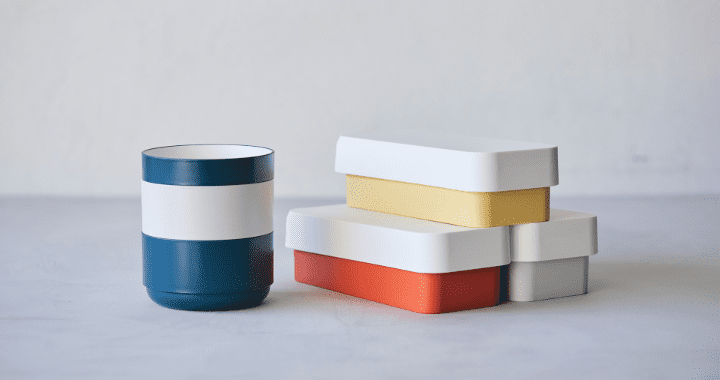
"Challenge to modern lacquerware" by utilizing traditional techniques
Yamanaka Lacquerware was one of the first companies to produce modern lacquerware by applying a urethane coating to a plastic resin base after World War II. While utilising the advanced painting and makie techniques developed through traditional techniques, Yamanaka Lacquerware produces a variety of tableware products that are not limited to traditional wooden lacquerware but are suited to modern life.
About Yamanaka NuriHistory
Around 1958, the production of modern lacquerware began, incorporating plastic materials in addition to wooden lacquerware. Today, it has spread to a wide range of fields as tableware, interior goods and bridal gifts.