Woodworker Shoji Mukaide
Delicate bark vessels are carved from rough-hewn wood.
After graduating from high school, he apprenticed himself to his father, a woodworker, and has been a craftsman for 39 years. No matter how much experience he has, days still come when things go wrong.
The character of the wood, the tone of the tools, the condition of the people. No two days are the same. That's why I'm so happy when I get a good piece of wood, I can't stop."
They use 50-60 KANNA(grinding blades) to produce bowls, plates, lidded containers (natsume) and other objects of all shapes and sizes. The technique of sen-suji, which produces fine concentric circle patterns, is the best among Yamanaka's woodworkers. Mukade's belief is that he only produces pieces that he can deliver to customers with confidence.
If I can't do something satisfactory, that's my current ability. I do my own research, and if I don't understand something, I ask fellow craftsmen to teach me. Every day is a serious battle."
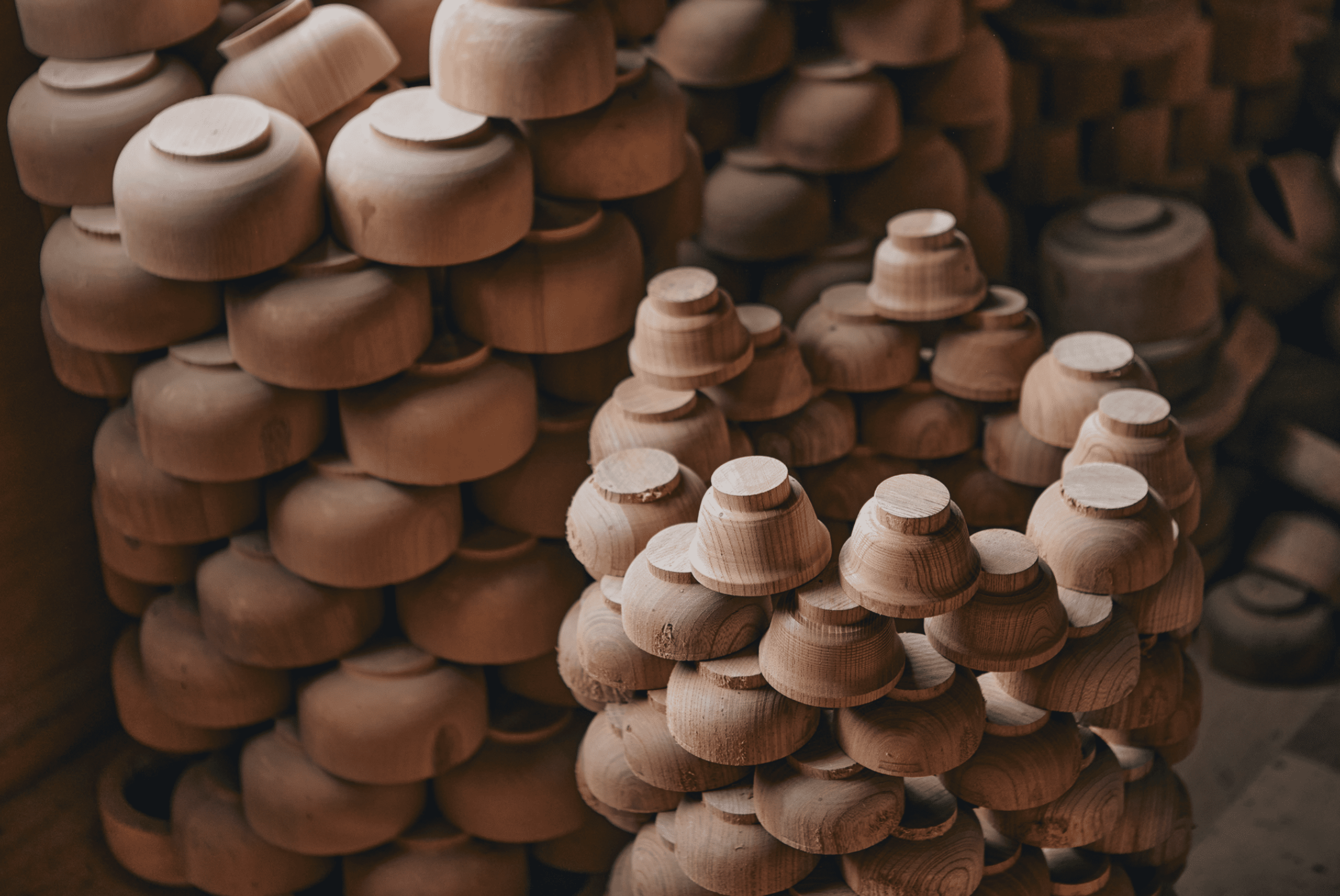
Vessels piled up to drain. Dry well in the workshop for about a month.
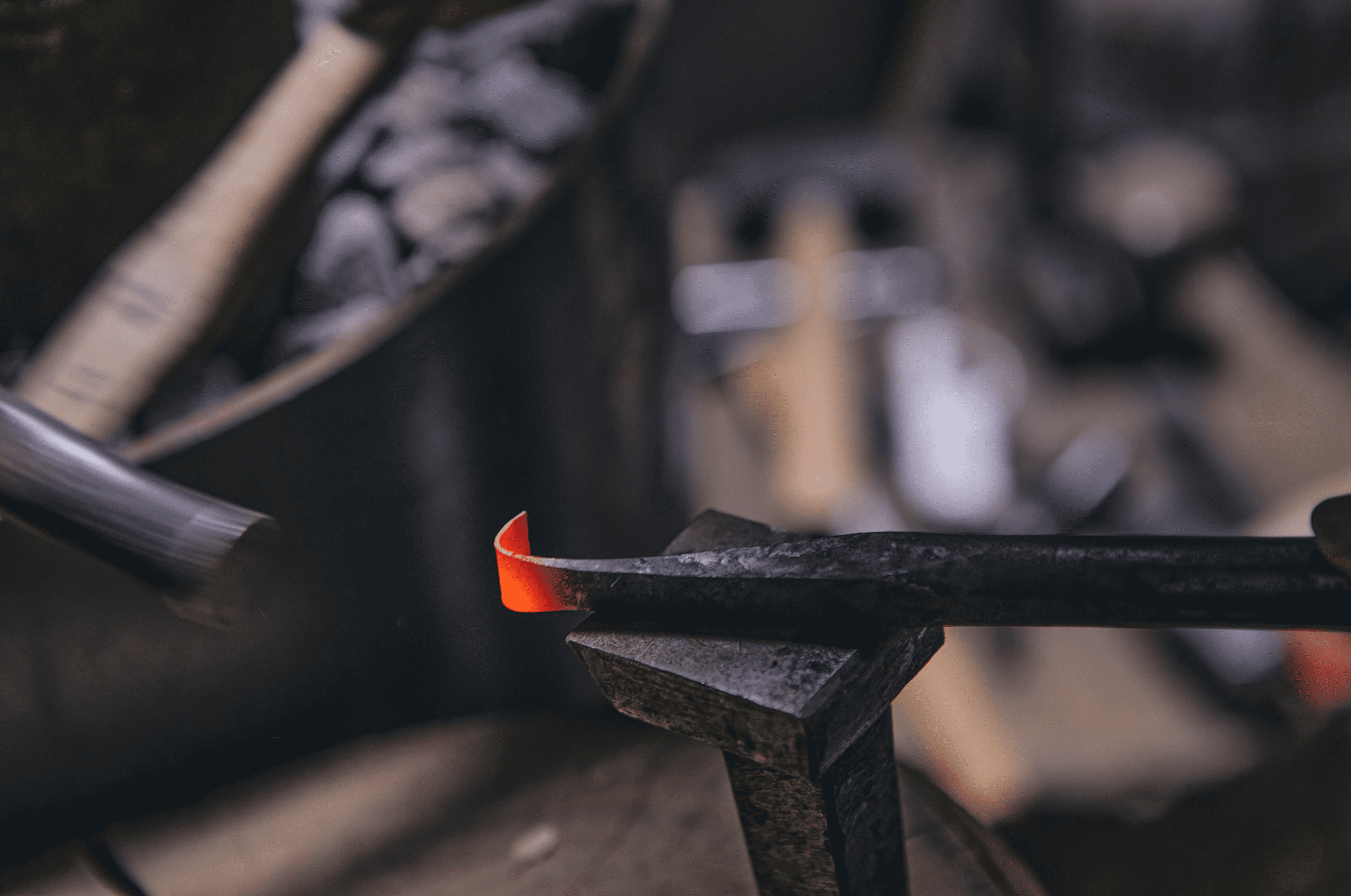
Steel (hagane) is heated in a cylinder, hammered and forged to form and make blades for yourself.
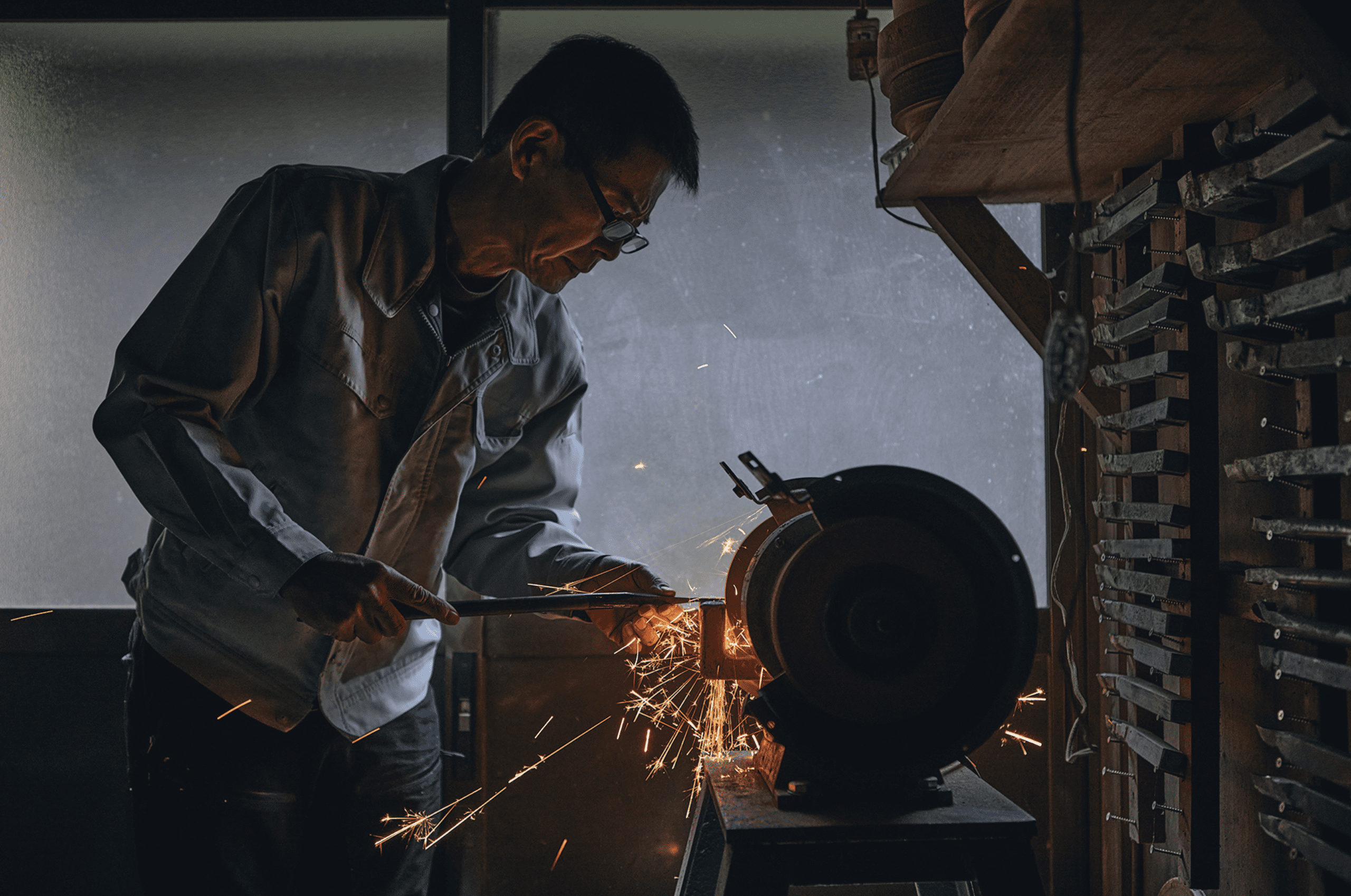
The thinner the blade edge, the better the sharpness of the blade.
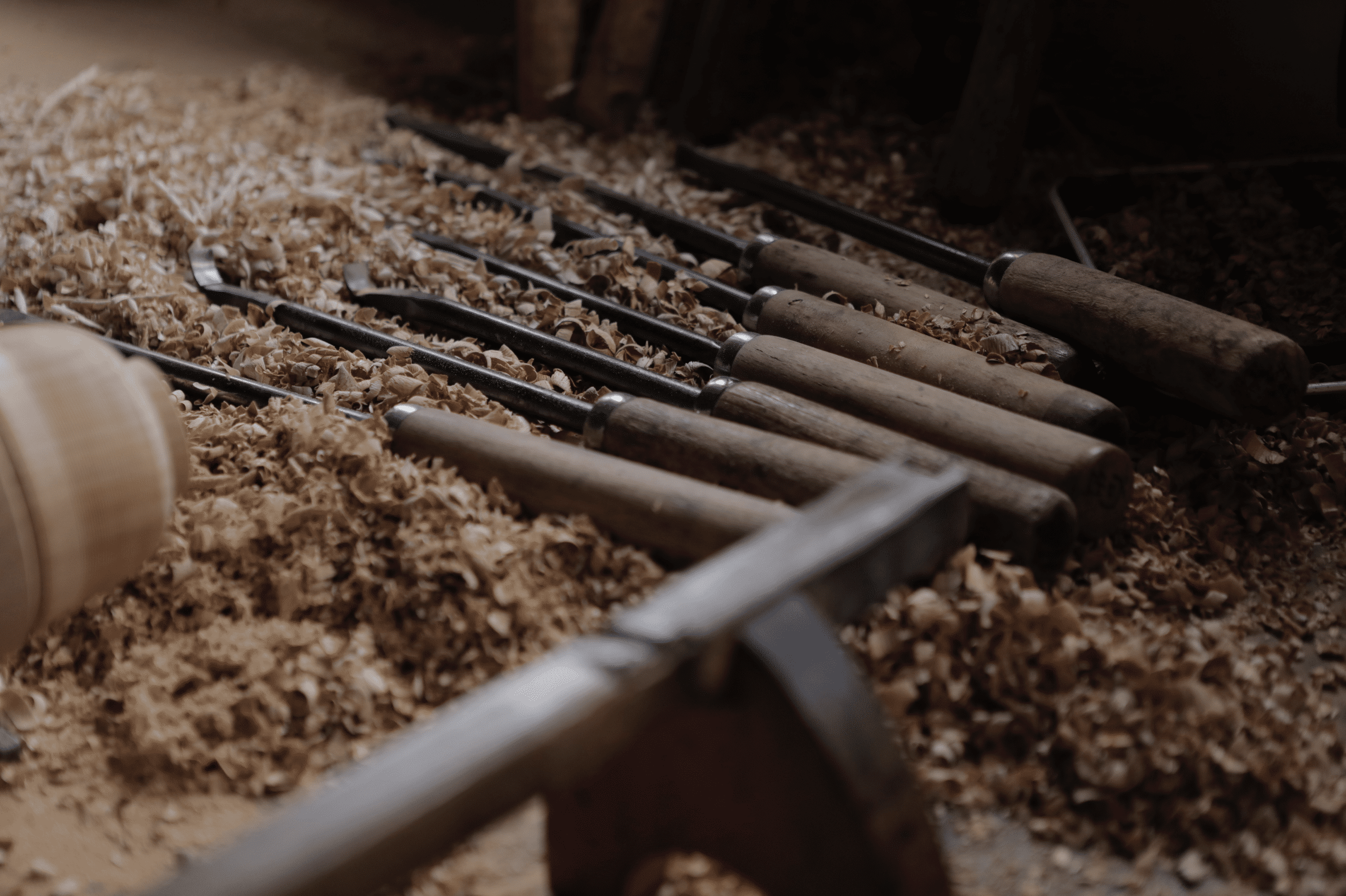
Each of the 50-60 cannas has a blade edge that is all different in size, thinness and roundness.
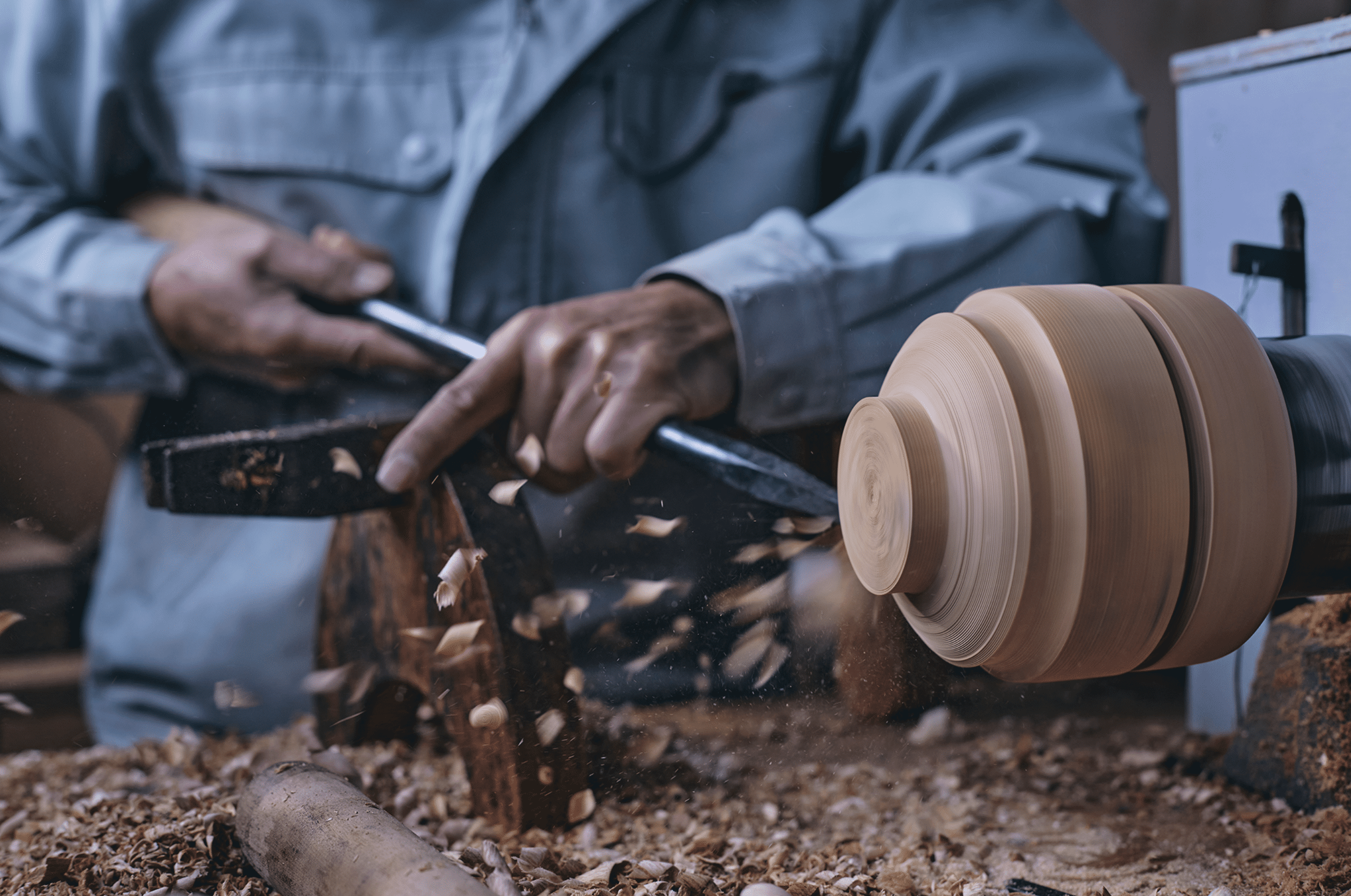
The way the shape of the vessel is carved out of a block of wood is truly a craftsman's art. They use a nationally rare wheel called a 'yokoza-shiki', which is suitable for grinding wood that has been cut vertically.
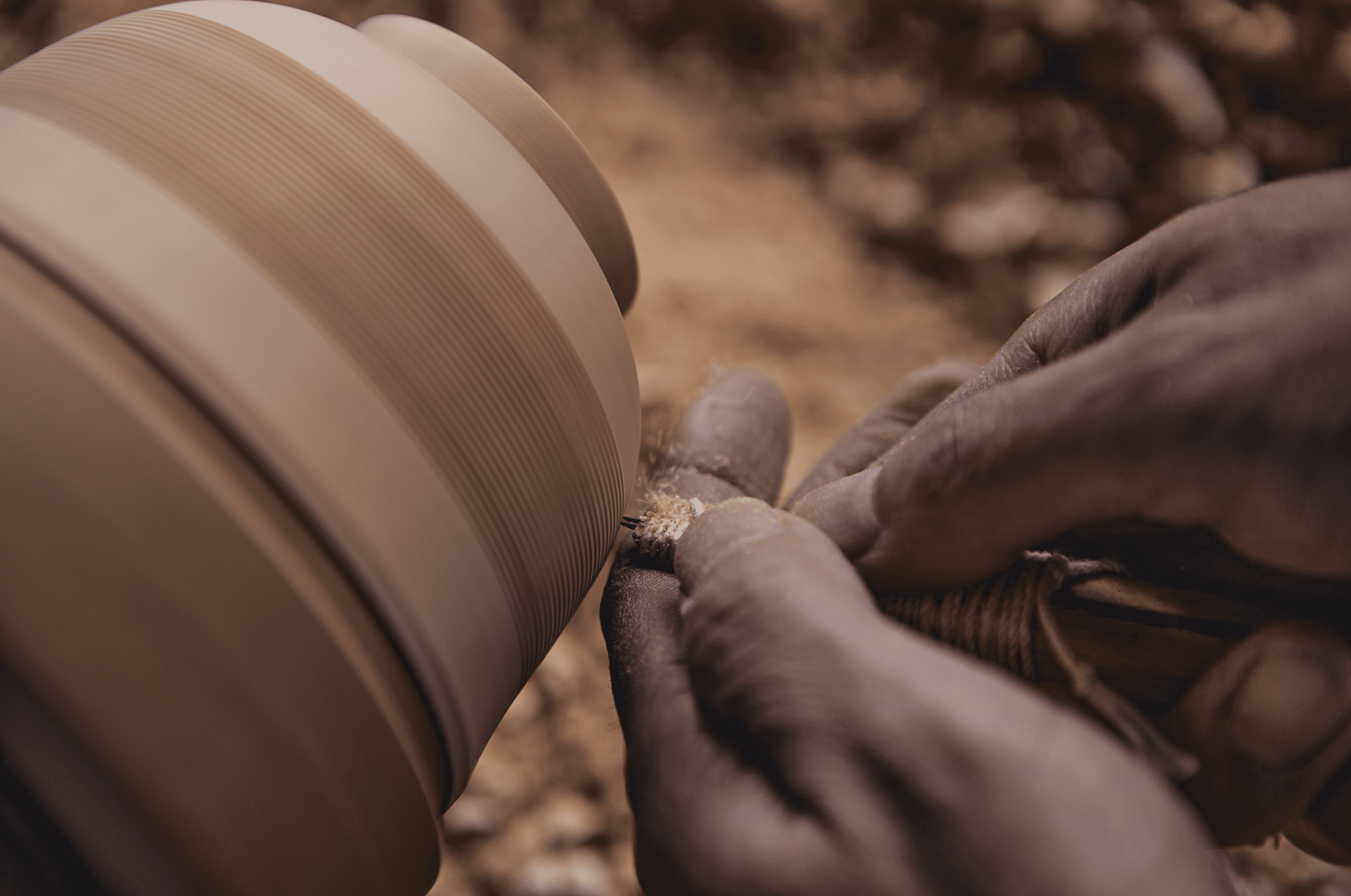
Decorative grinding is one of the traditional characteristics of Yamanaka lacquerware. A fine pattern is made using a wheel.
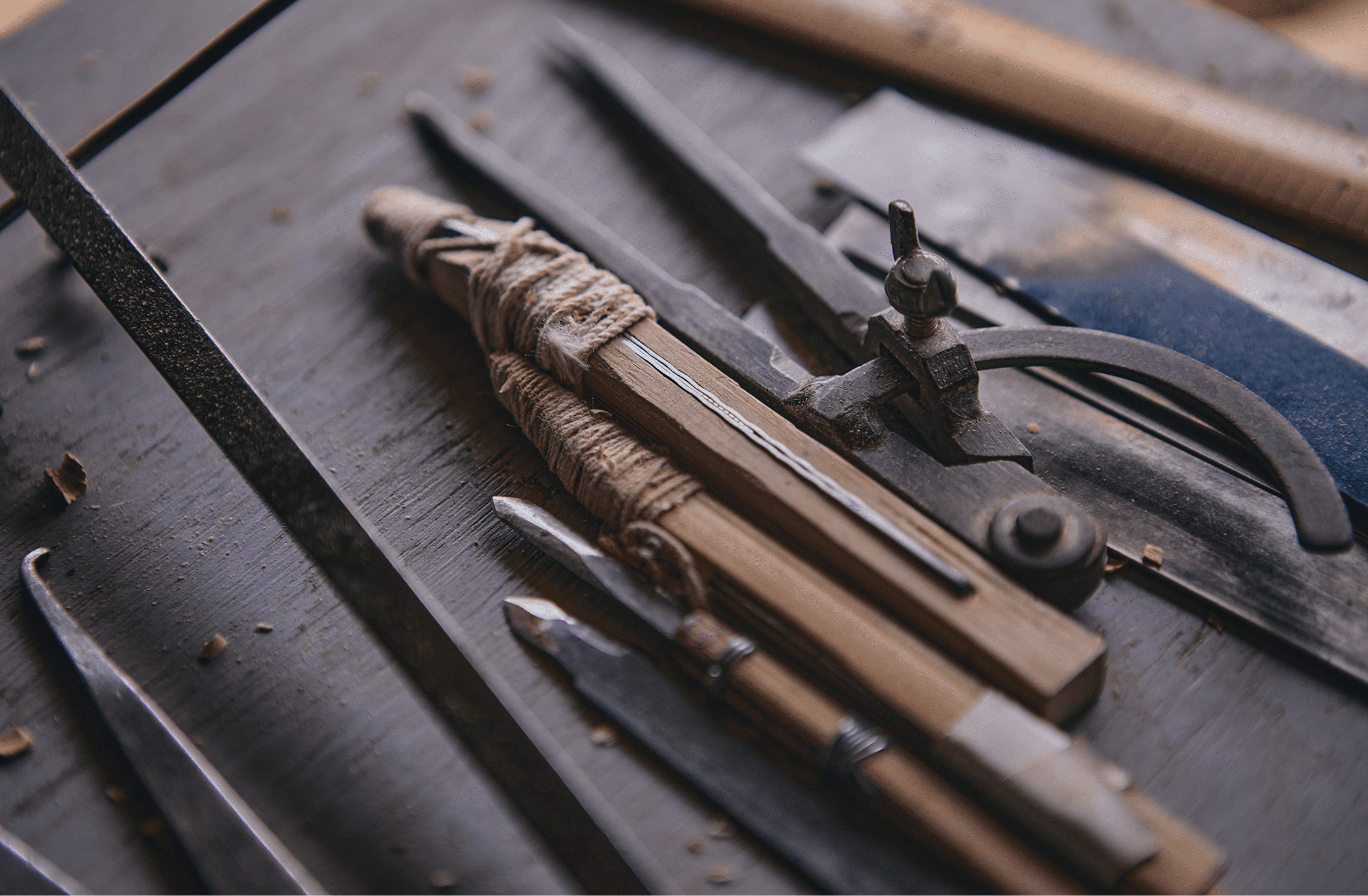
Tool used for decorative grinding. Two small knives with a metal saw blade between them are used for making sen-suji.
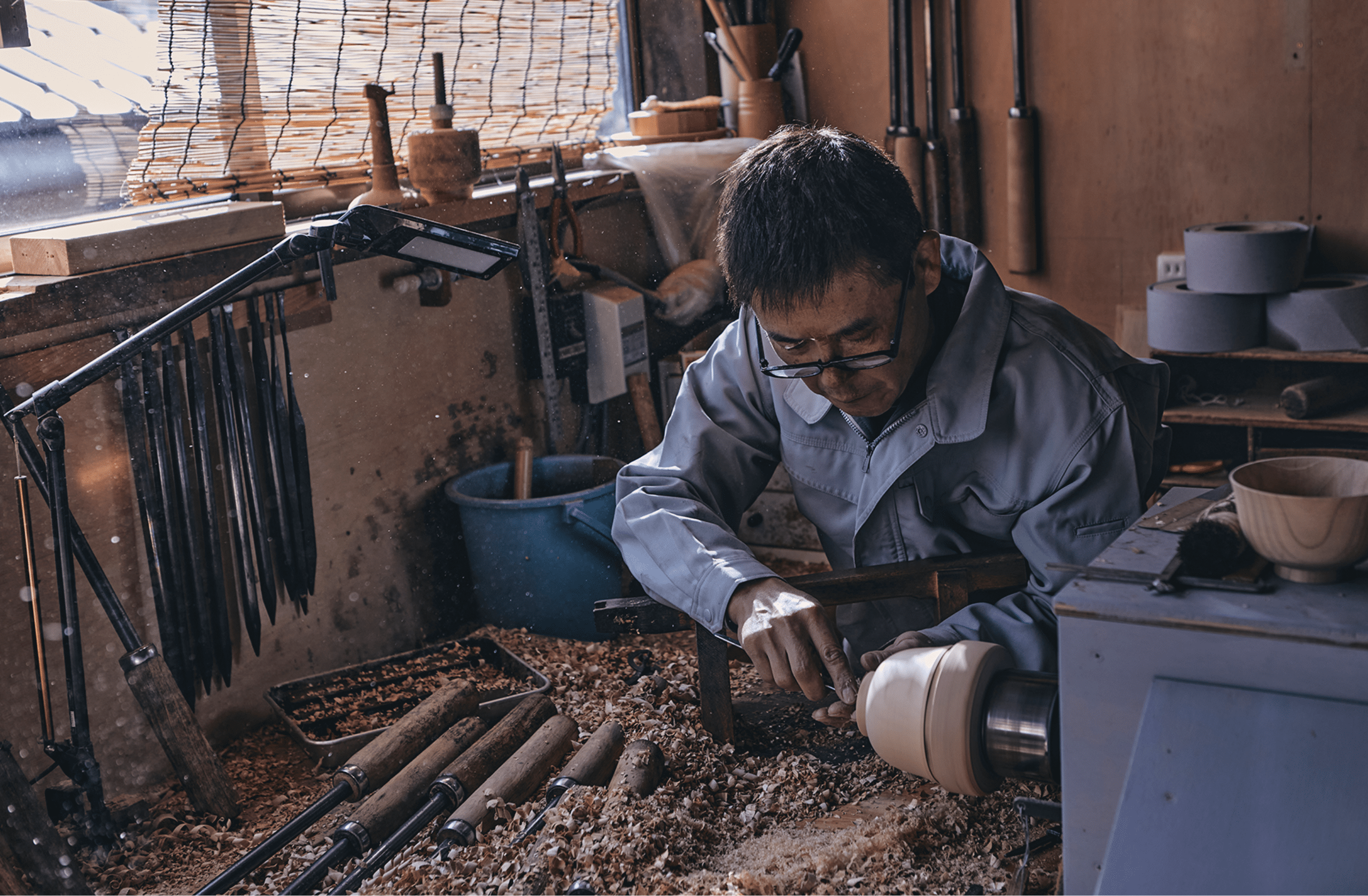
There are about 30 woodworkers active in the mountains. They meet regularly to exchange their skills and knowledge with each other.