Yamanaka CraftsmanManufacturing process
Lacquerware is produced through the division of labour. Once the lacquerware dealer (wholesaler) has decided on a design, a woodworker grinds the wood, and after a groundwork process, the lacquer is applied in coats of undercoat, middle coat and top coat, and then finished with the addition of makie (gold lacquer). This section introduces the production process of both traditional wooden lacquerware and modern lacquerware developed since the post-war period.
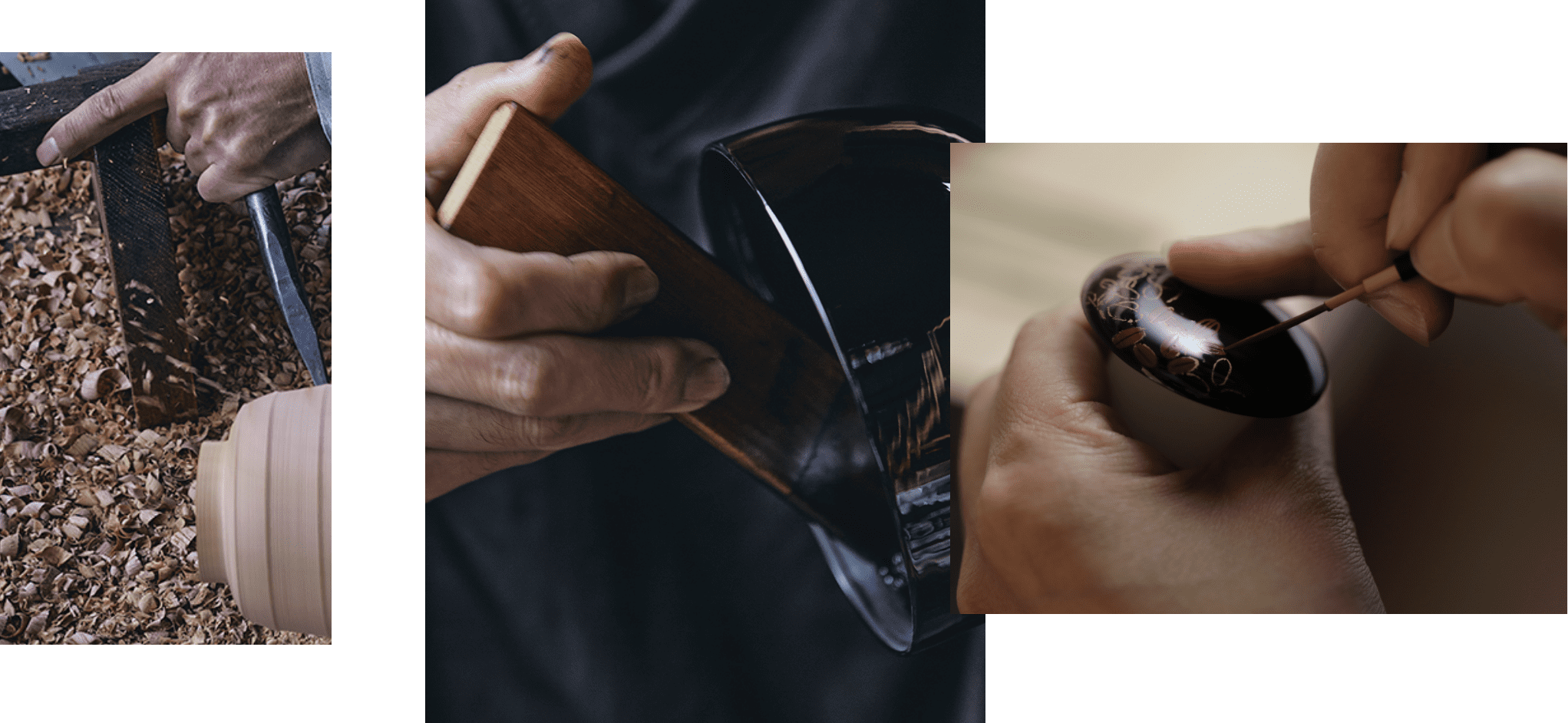
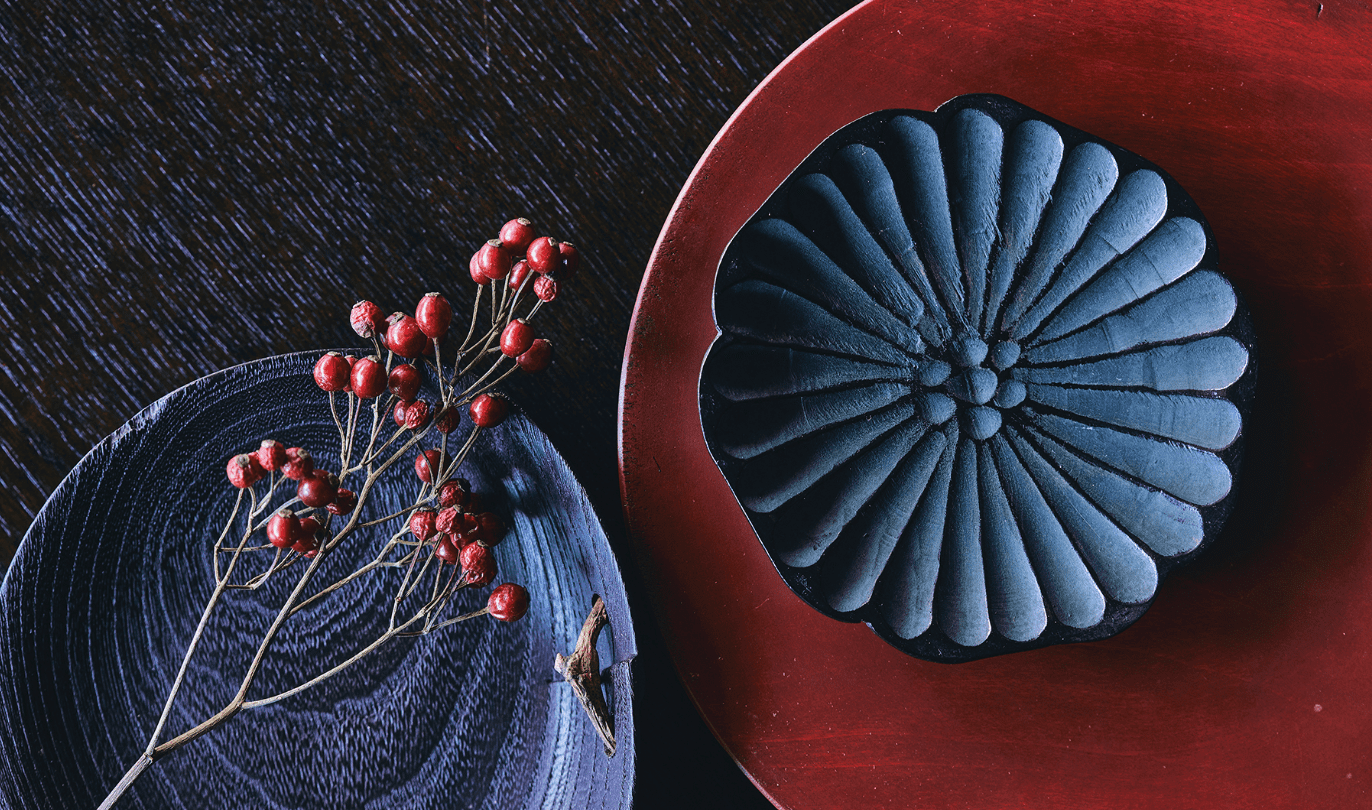
Wooden lacquerware
In addition to Shin-nuri, which involves the base and top coat processes described here, Yamanaka-nuri also has a characteristic technique called Wuki urushi (wiping lacquer) finishing. The lacquer is soaked into a cloth and rubbed into the wood by repeatedly wiping the cloth, which accentuates the delicate beauty of the wood surface.
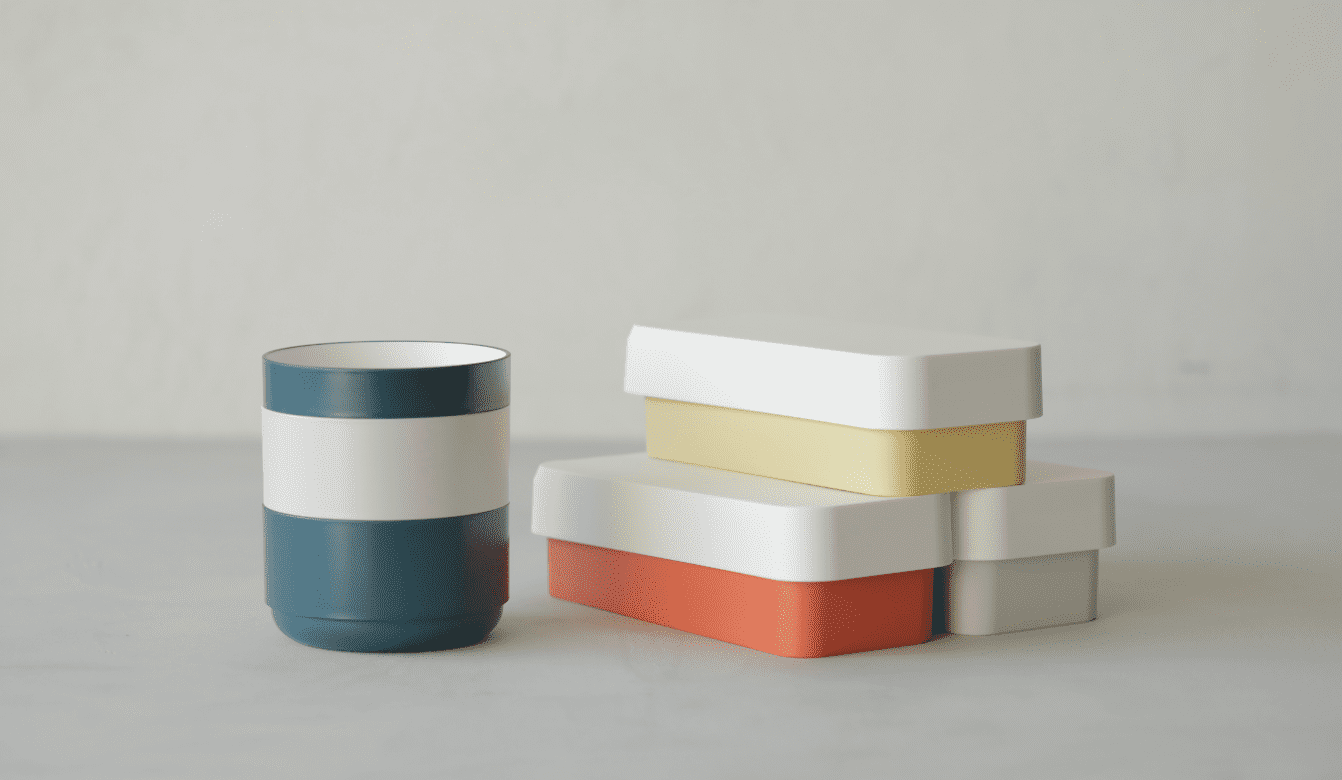
Modern lacquerware
Modern lacquerware is a product that uses plastic (resin) as its main material. In addition to rationality, durability and ease of maintenance, which cannot be achieved with wood alone, it is used in a variety of interior spaces, making the most of its freedom in terms of shape and colour. Today, they are also used as tableware for school lunches.